제조 및 개발 분야에서 티타늄 소재 응용 분야의 격차를 메우는 AI의 역할
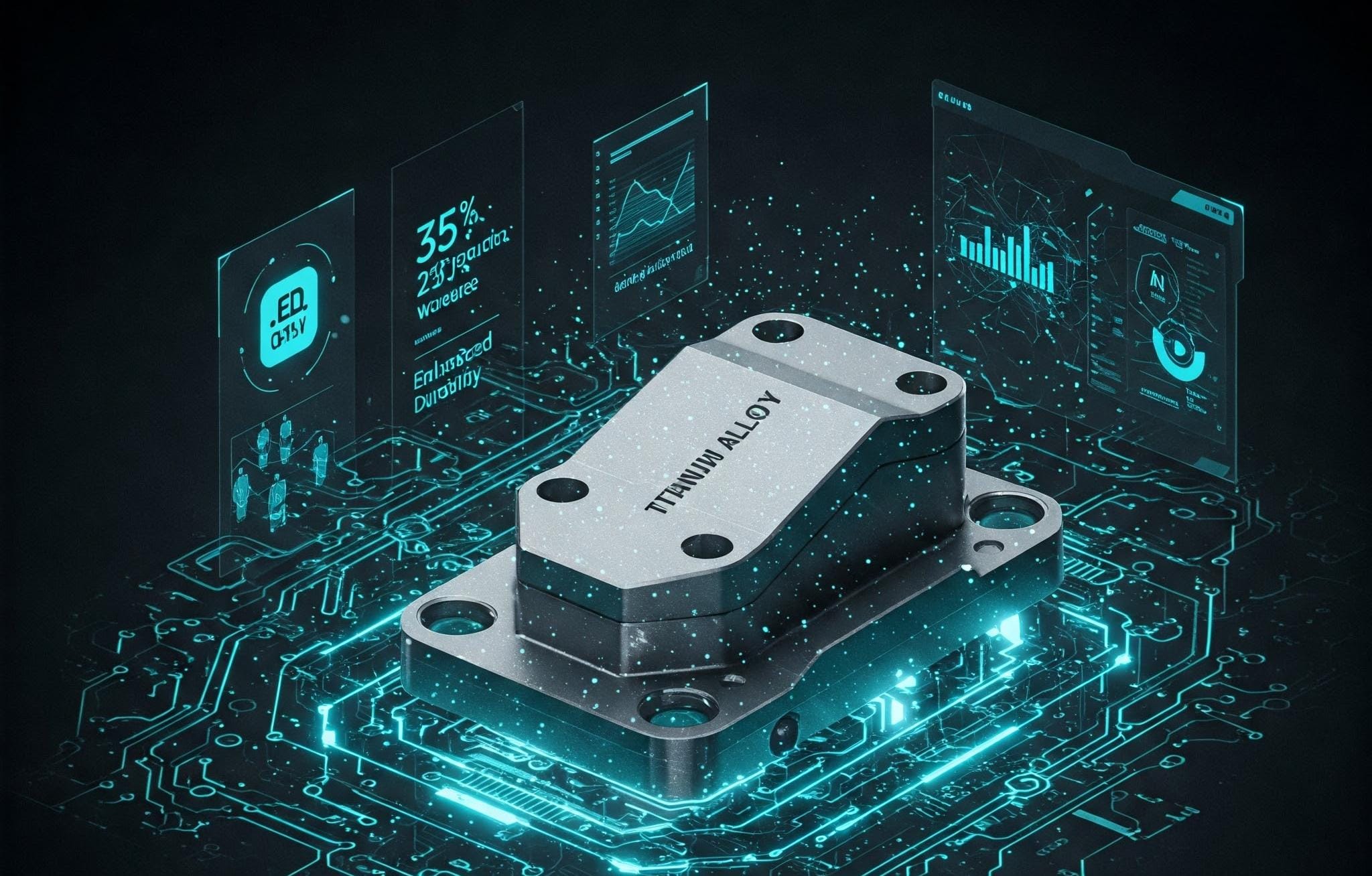
Date: March 10, 2025
Recent advancements in artificial intelligence (AI) have positioned it as a transformative force in the manufacturing and development of titanium materials, a global hot topic as of early 2025. Titanium alloys, prized for their strength-to-weight ratio, corrosion resistance, and biocompatibility, are critical in aerospace, biomedical, and automotive industries. However, challenges such as slow production processes, high costs, and material optimization have historically limited their potential. Updated research highlights how AI is closing these gaps, revolutionizing titanium applications.
Key Findings from Recent Studies:
1.Accelerated Production: A March 2025 study from Johns Hopkins Applied Physics Laboratory (APL) demonstrates AI-driven models optimizing laser powder bed fusion, a 3D-printing technique for titanium alloys like Ti-6Al-4V. By analyzing vast processing parameters, AI slashes the trial-and-error time from months to days, boosting production speed by up to 30% while enhancing strength and ductility. This addresses the gap of slow, resource-intensive manufacturing, critical for aerospace and submarine components.
2.Material Optimization: MIT’s 2024 research, expanded in 2025, shows AI identifying novel titanium alloy compositions with superior strength-ductility balances. Machine learning (ML) predicts atomic-scale phase interactions, reducing the reliance on costly iterative testing. This closes the gap in designing alloys tailored for extreme environments, such as space or deep-sea applications.
3.Cost Reduction: Additive manufacturing (AM) studies from 2023-2025, consolidated in a Frontiers review, reveal AI improving material utilization rates by 20-25% over traditional methods. By minimizing waste and energy use, AI tackles the high-cost barrier, making titanium more viable for automotive and medical implants.
4.Defect Prediction and Quality Control: Research from the Whiting School of Engineering (2025) integrates AI simulations to predict defects in AM titanium parts. This reduces failure rates by 15%, bridging the gap in achieving consistent high-quality production for biomedical devices and aviation.
Disappearing Gaps:
Time: AI slashes development timelines, enabling rapid prototyping and deployment.
Cost: Enhanced efficiency and reduced waste lower the economic threshold for titanium use.
Performance: AI unlocks new alloy properties, meeting stringent industry demands.
Conclusion: AI is erasing long-standing barriers in titanium manufacturing and development, aligning with global sustainability and innovation goals. As research progresses, expect wider adoption across industries, driven by faster, cheaper, and stronger titanium solutions.